OUR VEHICLE FROM 2022
After not having built a new vehicle since 2019, we have set ourselves clear goals in the beginning of 2021. Not only did we want to build a completely new vehicle that should, in terms of energy efficiency, outperform any Urban Concept we have ever built. We also aimed to build a completely new team that should be more international and diverse, to allow for more technical innovation through intercultural and interdisciplinary cooperation. We have clearly achieved our goals.
The new vehicle, muc022, is the result of more than 18 months of development, design, production, and testing. With an outstandingly successful participation in the efficiency competition Shell Eco-Marathon 2022, this car shows how a hyper-efficient urban vehicle could look like. Furthermore, we have successfully integrated an autonomous driving system that should, in the future, make driving even more energy efficient.
muc022
The Technical Features of the Vehicle
Key Data
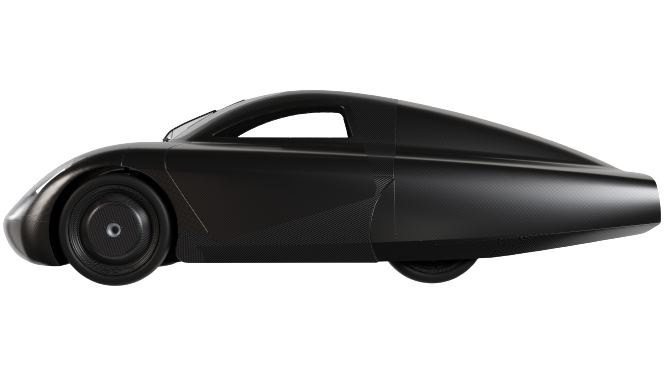
CFRP rims:
- -50% weight compared to previously used aluminum rims
System Voltage:
- 48V, monitored by self-developed BMS
Length/Width/Height:
- 3400mm/1200mm/1000mm
- Implementing a safe environment for production, including trainings and SOPs
- Safe vehicle body: the monocoque has a high strength and is dimensioned to form a rigid shell around the driver
The award is given to the most innovative design solutions that push the boundaries of energy efficiency.
- Electrical Powertrain: As one of only few teams we use a permanent magnet synchronous motor with a new, completely self-developed inverter
- Newly dimensioned and designed planetary gear set for speed reduction from motor to wheel with optimized tooth geometry for efficiency
- For the first time on a TUfast Eco Urban Concept: Carbon Fiber Rims, completely self-developed and built by the team, weight reduction of almost 50%
- New CFRP Monocoque, completely self–developed and built by the whole team using
CFRP Tools and state–of–the–art manufacturing techniques - New, more aerodynamic, vehicle outer shape, possible due to new monocoque →
half the drag force compared to muc019 - New drivetrain and gearbox topology with gearings optimized for efficiency
- New suspension system: kinematics changed, new topology optimized uprights and
suspension mounts
The award is given to the best usage of simulation and optimization software tools to increase efficiency of the design process as well as the product muc022.
- Model-in-the-Loop Simulation for our Inverter Field oriented Control (Matlab/Simulink)
- Topology Optimization for Uprights and Suspension Mounts(AltairInspire)
- Multibody Simulation for the Suspension System (Altair)
- Structural Finite Element Analysis for Metal and Carbon Fiber Composite Parts (Altair Hyperworks)
- Lay-Up optimization for the Monocoque (AltairHyperworks)
- CFD Simulation to determine the vehicle outer shape (StarCCM+)
Electrics & Electronics
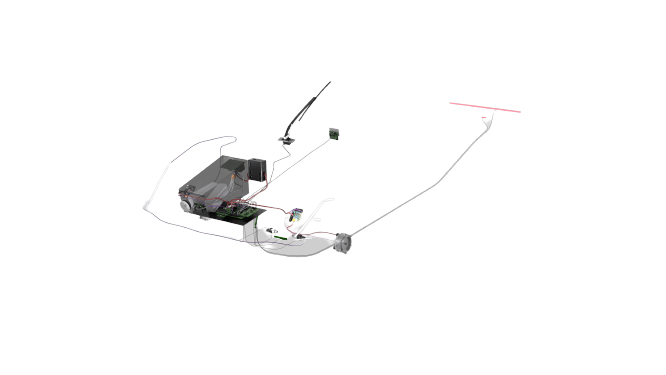
Human Machine Interface:
- Â LCD memory display with display controller, input buttons and troque setting paddle shifters
Efficiency Optimized Power Train:
- 2 x 440W permanent magnet synchronous motors with torque controlling gallium nitride frequency inverters and MTPA control algorithm
Power Supply System:
- Battery Management System providing cell voltage monitoring, temperature monitoring and over current protection for 4000, 5000 and 21000 mAh lithium polymer batteries
Vehicle System Control:
- Â Main Control Unit for LED head- and backlights, steering indicators, windscreen wiper, brake pressure monitoring and horn
Vehicle Body
Better Material:Â
- Carbon Fiber Composite Material using only Prepreg (state-of-the- art)
Improved Aerodynamics:
- Immense drag reduction compared to previous vehicle (- 50%)
New Monocoque:
- Enabler for aerodynamic shape with optimized layer structure including aluminum honeycomb
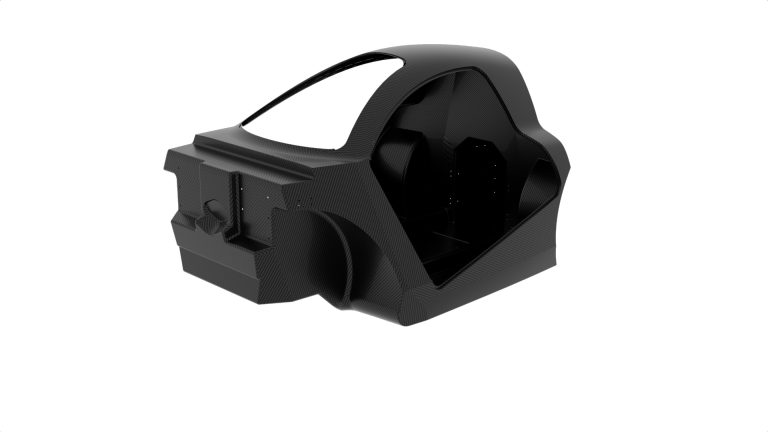
The whole Eco-Team helped in manufacturing of the Carbon Fiber Parts, especially the monocoque. Using a comprehensive shift system with up to 4 shifts per day, the team first cut and glued epoxy blocks which were then machined into shape by our sponsors. After sanding these patterns, we prepared them chemically for either laminating carbon fiber toolings (monocoque) or directly laminating final parts. For the monocoque, we then assembled the toolings into one negative mold for then being able to laminate the final part. Every time we needed to harden and consolidate the carbon fiber prepreg to form a tooling or final part, we had to build vacuum bags to then bring them to sponsors for the autoclave process.
Suspension System
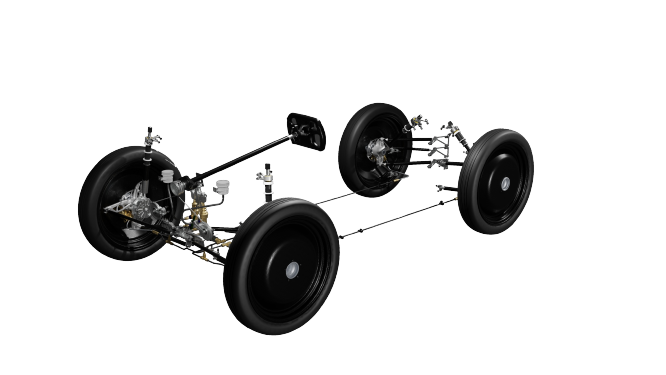
Topology Optimization:
- Uprights and Suspension Mounts-high stiffness, minimal weight
Kinematics:
- MacPherson in the front, double wish bone in the rear
Vertical Dynamics:
- Elastomer Springs in the front and rear combine spring and damper function in ultralight package
Drivetrain:
- Fully integrated in Front Uprights, New Planetary Gear Set with optimized teeth geometry
Steering:
- Ultralight, cable-operated, including autonomous actuator that can be easily detached
Brakes:
- Dual-circuit, four-disc hydraulic brake system optimized for low weight
Autonomous System
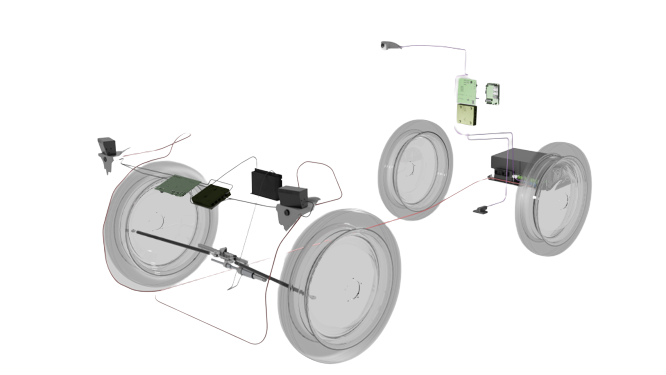
Perception:
- LIDAR and Camera based 3D object and environment detection, Neural Networks for Image-Based track recognition
Planning:
- Time and distance optimized software for fast and agile local and global planning, Clever Usage of Model Predictive Control Approach in Planning
Control:
- Lateral and Longitudinal Vehicle Control (steering actuator and electric motors) by self-developed software written in Matlab/Simulink
Software Development:
- CI/CD for fast prototyping and integration on the vehicle, Simulation in CoppeliaSim for virtual validation of software stack and preparation for challenges on the competition