OUR VEHICLE FROM 2023
Create. Evolve. Thrive.
This was the mantra of our season. Coming from a very successful previous year, we set out to bring the new urban concept vehicle muc023 to the limits of current technology. We aimed to reach for greatness in the way we always have; through engineering creativity, operational ingenuity and commitment to our vision.
A diverse team formed with specializations in electrical engineering, management, mechanical engineering, and computer science. Together, we’ve not only built a car that goes to the limit of efficiency, but also one that boasts advanced self-driving capabilities. After countless hours in the workshop, we headed out to our competition in France to put our car to the test against many student teams from across the world.
There, we once more were able to achieve great success and cemented our status as one of the most competitive teams of the Shell Eco-marathon.
Coming back to our home town in Munich we felt some relief after the completion of this project, but also incoming nostalgia remembering the great times we had during the season. The vehicle of 2023 is the pride of over 80 interdisciplinary students, who poured their heart into the car.
Welcome to the future of driving. This is muc023.
muc023
The Technical Features of the Vehicle
Key Data
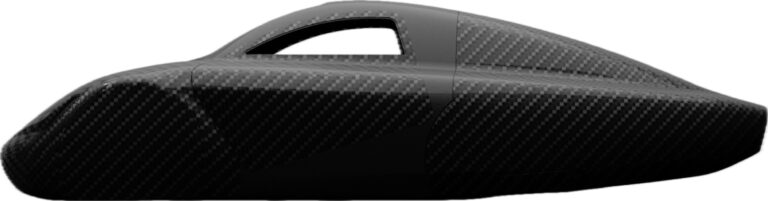
Covered front wheels:
- All four wheels covered for the first time in the history of TUfast.
One motor propulsion:
- Rear-wheel permanent magnet synchronous motor (PMSM).
Length/Width/Height:
- 3400mm/1300mm/1000mm.
The award is given to teams who actively integrate safe practices in their production process.
- Certified safety instructions for all team members to access the workshops.
- Trainings by highly qualified partners for the operation of heavy machinery.
- Sufficient safety factors for simulated loads on the monocoque.
- Thickness & ply optimization to withstand all occuring driving forces.
- Fire safety, evacuation paths and emergency response plans for all events.
The award is given to the best usage of simulation and optimization software tools to increase efficiency of the vehicle and the design process.
- Driving strategy simulation factoring in height profile and pit stop requirements.
- Lubrication simulation for friction reduction in the gears.
- Aerodynamic CFD-simulations resulting in 18% drag reduction.
- Topology optimization, MBS and FEA for optimal lightweight design, pushing the cars weight to 65kg.
- Highly integrated PCB layout utilizing PDN Analyzer (Altair).
This prize recognizes the conceptual/actual design of intelligent information and knowledge processes for a data-driven competition approach.
- Monitored live data throughout the electrical system (BMS, MCU, etc).
- Recorded motor speed and temperature to optimize our simulations.
- Ensured safety through continuous brake pressure checks.
- Iterated our driving simulation with every new data point.
- Achieved energy consumption for telemetry of <1% of total power draw.
Â
Electrical
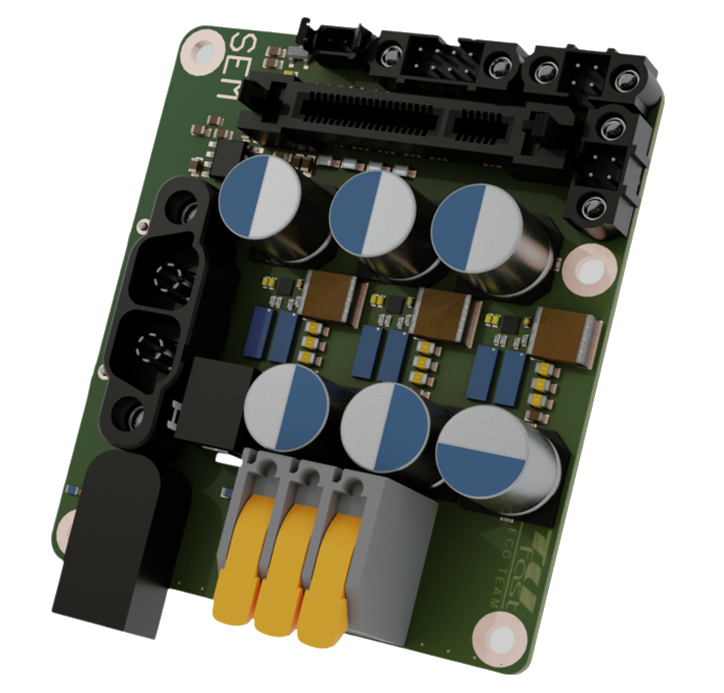
Motor:
- Permanent magnets synchronous motor (PMSM).
- Motor power: 1 x 570W / 0.77 hp.
- Peak motor torque: 12.7 Nm.
Motor Controller:
- Gallium nitride frequency inverter.
- MTPA current regulator.
Wonderboard:
- Extremely compact power control, distribution and logic unit.
Display:
- LCD Memory Display.
Our permanent magnet synchronous motor (PMSM) and GAN FET inverter technology define the highly efficient powertrain within our single wheel drive system, allowing us to achieve our desired track speed with less than one horsepower. In addition, power distribution network simulations have enabled us to create an extremely compact power control, distribution and logic unit called the Main Control Unit, or as we call it, the Wonderboard. It combines the functions previously performed by four different boards into a single PCB. This, together with a number of other new designs, has enabled us to reduce the total weight of the electrical system by more than half a kilogram, which also contributes to the car’s lightweight design and reduces power losses.
Vehicle Body
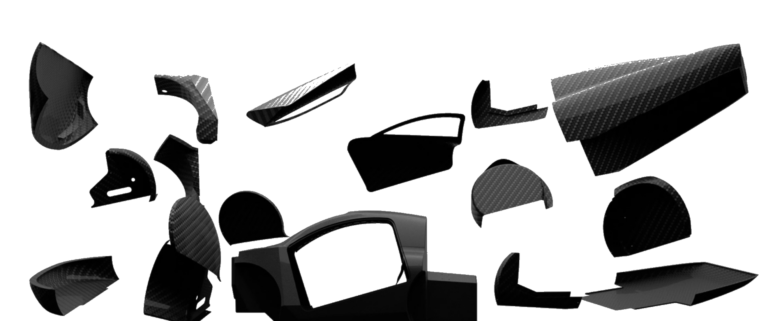
Aerodynamic Shape:
- Optimization of the vehicle’s aerodynamics through numerous iterative simulations.
- Use of new innovative technology: Adjoint-Optimization.
Carbon Fiber Monocoque:
- Complete passenger cell made of carbon fiber composites with an aluminum honeycomb sandwich structure.
- Thickness optimization of carbon layers and aluminum core material through simulations of multiple load cases.
- Total Monocoque weight of only 14.7 kg.
High-Tech Materials:
- Use of state-of-the-art carbon fiber for the entire body.
- Lowest weight with simultaneously high stiffness.
Design and Manufacturing:
- Development of a vehicle body oriented to urban use with a super aerodynamic shape.
- Carbon body parts manufactured by the team.
One of the key focuses of the vehicle is aerodynamics. The goal this season was to reduce air resistance to the possible minimum for this concept. Over months, the shape of the outer shell was iteratively modified and verified through our CFD simulations. We approached this by reducing the drag coefficient, which was already at a low value of 0.16 in the predecessor. After more than 30 simulations and an innovative simulation method called Adjoint Optimization applied at the end, we were able to reduce air resistance by almost 30% compared to the predecessor, achieving a Cw-value of 0.13 – the lowest ever at TUfast.Â
Suspension System
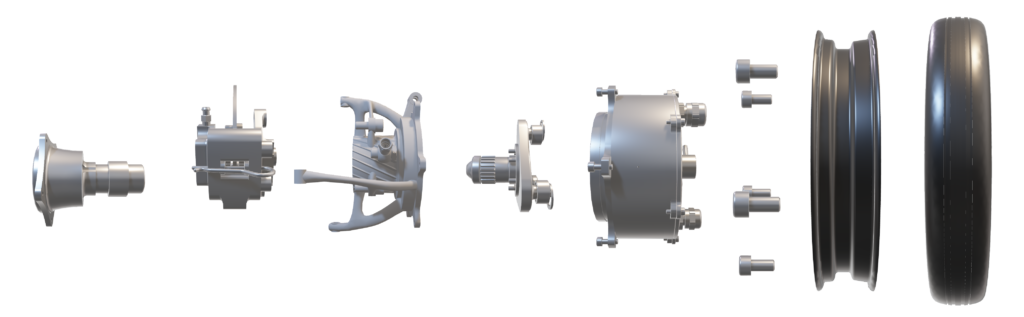
Topology Optimization:
- Uprights, Suspension Mounts and Brake Pedal – varying materials and techniques for different wall thicknesses and part sizes, minimizing weight while maintaining maximum stiffness.
Kinematics and Vertical Dynamics:
- MacPherson strut in the front axle and Double wishbone suspension in the rear axle using elastomers to combine spring and damper functions in ultralight package.
Drivetrain:
- One fully integrated motor and drivetrain assembly with newly developed Planetary Gear Set with optimized teeth geometry and lubricating agent in Rear Upright. Interchangeable in side for additional control of weight positioning dependent on track.
Steering:
- Ultralight, cable-operated, including easy-to-install rotational motor at the end of the steering shaft for autonomous driving.
Brakes:
- Four-disc hydraulic brake system with dual-circuit in X-formation. Optimized for low weight with chosen materials and pedal design.
- What is topology optimization?
Topology optimization is a design process that utilizes a feedback loop between itself and stiffness simulations to generate optimal material distribution within a given design space. Its goal is to maximize performance while minimizing material usage, resulting in lightweight and efficient structures. - How do we produce these parts?
These parts are produced through advanced additive manufacturing techniques like 3D printing and selective laser sintering. With these processes, we could create complex geometries with optimized material distribution. - What parts do you have optimized and Sintered in your car?
In our car, we have optimized and sintered the uprights, suspension mounts, brake pedal, and more. - What materials do you use when metal sintering?
These components have been designed using varying materials and techniques accounting for wall thicknesses and part sizes as well as weight saving opportunities, ultimately reducing weight while maintaining stiffness. - What was the weight reduction acchieved with the processes used compared to traditional manufacturing techniques?
The weight reduction achieved through these processes is significant. In the suspension metal mounts, we’ve achieved a reduction of more than 40%, while the brake pedal has seen a remarkable 70% reduction in weight. This improvement represents approximately a 3kg reduction compared to traditional manufacturing techniques.
Autonomous
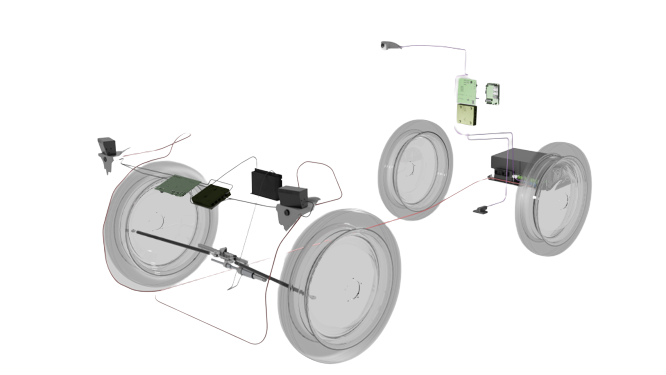
Sensors:
- 360° LiDAR and 5 Cameras on top of monocoque.
- 2 Solid State LiDAR paired with camera on each side of bonnet.
- Depth Camera in middle of bonnet
- Ultra high accuracy global positioning system, with two antennas.
Actuation:
- Direct drive motor attached to steering column with absolute positioning.
- Full access to drivetrain controlled by custom build inverter.
Processing:
- Purpose made rugged PC with high performance per watt.
- State of the art graphic accelerator card.
- Specialized video grabber card directly connected to cameras.
Software:
- Selfmade neuronal networks for image processing and analysis.
- In house pointcloud for combining camera and LiDAR data.
- High fidelity 3D Voxel based mapping system.
The autonomous system is a unique challenge for the whole team. While writing software is certainly the major part in developing a fully functioning driverless car, software alone cannot steer the car. It takes skilled electrical engineers to design PCB for controlling the motor and knowledgeable mechanical engineers to ensure no part not intended for movement yields when steering with high forces.
Generally, all components required for autonomous driving have to be attached to the car somehow and simultaneously be provided with data and power. This drives our autonomous team to work closely with other disciplines to realize our dream of full autonomous driving.